Cob continues to be a widely used building material, especially in the UK where it can be found along the Scottish borders, East Anglia, The Midlands, and the West Country, where between East Cornwall through to Wiltshire it is at its greatest concentration.Â
Cob typically consists of sub-soil containing small stones, straw and water. The cohesion is provided by the clay that is present in the sub soil, whilst the straw binds the mix into workable lumps and reduces the effects of cracking. 10% to 12% volume of water is typically added to the mixture to ensure it is pliable enough to build with.Â
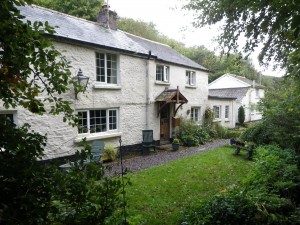
Despite the heavy use of water during the process of cob-making, excessive amounts of water ingress on cob walls is likely to be catastrophic. The water will result in the expansion of the clay particles subsequently weakening the cohesion between the aggregates. As a result, the wall will first be reduced to a plastic state before becoming liquidised, leading to structural failure.Â
As surveyors, a problem we often see is the use of cement renders on cob walls, creating damp issues and deterioration of the cob. Differential thermal expansion can cause the render to crack, which will allow moisture to penetrate and dissolve the cob behind. Although regularly checking cracks on the render and ensuring they are correctly filled may prevent any damage in the short run, the only permanent solution is to replace the cement with a flexible lime based render which ‘breathes’.Â
Cob chimneys are also a common source of damp, as the majority built before the war were done so without a horizontal damp proof course in place. As a result, excessive water ingress would cause the cob to deteriorate and, if not spotted soon enough, the chimney could collapse.Â
Damp issues may also be common at ground level, which are likely to build up around old buildings over time. If exterior ground levels rise above that of the internal floor finish, water is more likely to find a way into the building and cause damp. If it is possible to reduce the level of the ground around the cob building, this may be a suitable solution. However it is not often possible, so replacing the affected area of cob with a material less prone to failure under damp conditions may prove the most effective, though costly, solution.Â
It is common for people to jump to conclusions with regards to cob and especially the use of lime renders. It must be stated that plenty of cement renders will and have performed well when used in conjunction with cob possibly because it was common practice to ‘soften’ cement with hydrated lime to a ratio of 1:1:6 (lime:cement:sand).Â
It is important to be aware of the possible presence of cob especially if you are working or purchasing in one of the areas mentioned earlier in this article, where cob buildings are often found. Wall thicknesses can provide an indication, with thicknesses of between 400mm and 700mm not uncommon for cob structures. This is often confirmed by looking at the exposed wall head in the loft area.Â
Most importantly the use of cob must not be feared, just understood. If you require more information about cob, are concerned your cob building may be suffering from water ingress or are simply buying a house that you think may be of cob construction, contact a local chartered surveyor who will be able to provide you with professional advice.Â
BT/SRJ Â Â Â Â Â Â Â Â Â Â Â Â Â Â Â Â Â Â Â Â Â Â Â Â Â Â Â Â Â Â Â Â Â Â Â Â Â Â Â Â Â Â Â Â Â Â Â Â Â Â Â Â Â Â Â Â Â Â Â Â Â Â Â Â Â 1/05/14